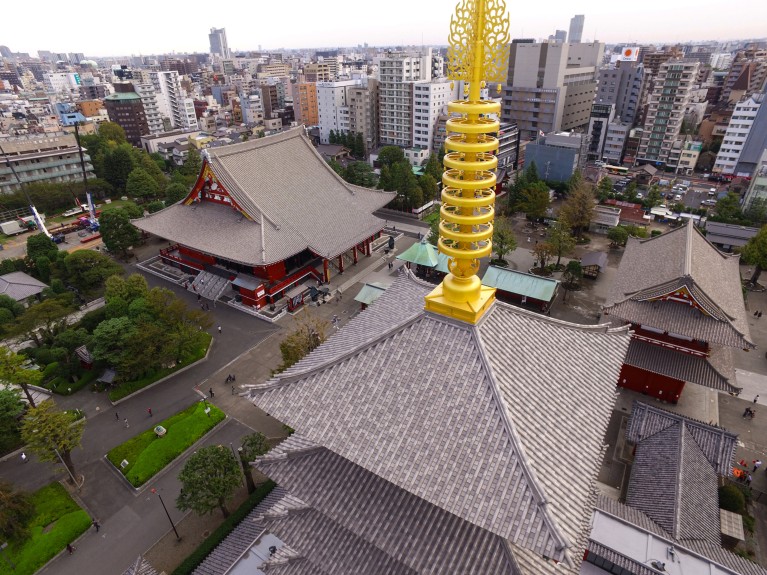
Titanium’s combination of high strength, high corrosion resistance and low weight increases the earthquake-resistance of architectural buildings while keeping the appearance of traditional Japanese roof tiles.© CANAME co.,ltd
From the sweeping roofs of Sensoji temple in Tokyo to the swooping forms of modern-day jet aircraft, titanium metal’s renowned high strength, low weight and high corrosion resistance are finding increasing use every year. Titanium is widely available in minerals and ores — the white pigment in most house paint is based on titanium dioxide. However, smelting and purifying titanium requires specialized, high-temperature treatments that add much to its final price tag and release copious amounts of carbon dioxide into the atmosphere.
The challenge of meeting rising demand while simultaneously reducing greenhouse-gas emissions continues to vex titanium manufacturers worldwide. A new smelting technology developed by Japan’s Toho Titanium in cooperation with Universal Achemetal Titanium, LLC (UAT) in the United States promises to resolve this dilemma by eliminating carbon from the extraction equation.
Pyrotechnic performance
Commercial titanium extraction is based upon an 80-year-old procedure developed by Luxembourg-born chemist William Kroll. Powdered titanium dioxide ore is placed in a smelter containing chlorine gas and the carbon-based reducer known as coke. Temperatures of around 1,000 degrees Celsius then produce liquid titanium tetrachloride as well as carbon dioxide gas as a by-product. The titanium tetrachloride is subjected to another high-temperature treatment with magnesium to release pure titanium metal as porous structures called sponges that are subsequently melted into ingots and converted through wrought processes into structures such as plates, sheets, wire and rods.
Researchers have been working on alternatives to the Kroll process for decades, says Hideki Fujii, executive managing officer of Toho Titanium. However, most of these systems are not economically competitive with well-established production routes and they produce lower quality titanium.
“Producing a tonne of titanium can emit around 10 tonnes of carbon dioxide gas in the current routes,” says Fujii. “Titanium costs will drastically increase in countries that have implemented a carbon tax. There are lots of proposals for titanium smelting, but most of them do not have an effective way to refine the metal — this is one reason why new smelting technology has not been commercialized for years.”
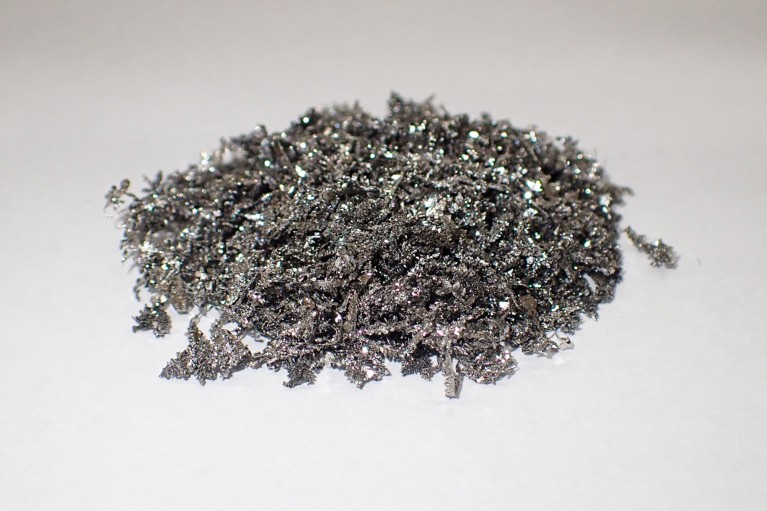
An image of a dendritic-shaped deposit on a cathode. © TOHO TITANIUM CO., LTD.
Fujii and his colleagues identified a promising approach developed by UAT as a way around conventional extraction bottlenecks. In the UAT method, powdered titanium dioxide ore is combined with calcium fluoride (known as fluorite) and aluminium metal. When this mixture is ignited, it undergoes a pyrotechnic thermite reaction that spontaneously raises the smelter temperature without using many external fuel sources.
The thermite reaction step leaves behind a floating slag of aluminium oxide and calcium fluoride that can be easily separated from solidified titanium alloy containing some oxygen and aluminium. A unique electro-refining process then dissolves mainly titanium from the titanium alloy into an electrolyte before it re-appears as a solid, dendritic-shaped deposit on a cathode. A final wash with water or a vacuum separation process yields titanium metal with a low impurity count equivalent to current commercially pure titanium.
“There are lots of advantages compared with the Kroll process,” says Fujii. “Because we don’t use carbon as a starting material, carbon dioxide emissions are no longer a problem. And electricity consumption is estimated to be reduced by 70% to 80% compared to standard titanium manufacturing.”
Deft piloting
After a successful lab trial, Toho Titanium is aiming to take their new extraction technology to another level in 2021. The company will construct pilot-scale facilities that feature electrolysis cells of different sizes in an effort to optimize the electro-refining process.
“A unique feature of our pilot setup is the gate valves in the middle of the electrolysis cells, says Fujii. “Once we’ve obtained the deposited titanium, we can lift the metal up to the valves, enabling us to easily separate the lower and upper portions.”
The company has found that improvements to the electro-refining procedure can significantly reduce impurities in titanium — a critical step that can broaden the market for this light, strong and durable metal.
“Titanium sponge produced by conventional process, which is the source of all titanium-based materials, usually contains about 0.02–0.05% oxygen. By using the electro-refining process, we can drop oxygen levels to around 0.03%, and other impurities to parts-per-million levels — almost to the limits of detection,” says Fujii. “That means we can widen the application range of our technology, from commercially pure titanium to almost all titanium-based materials.”
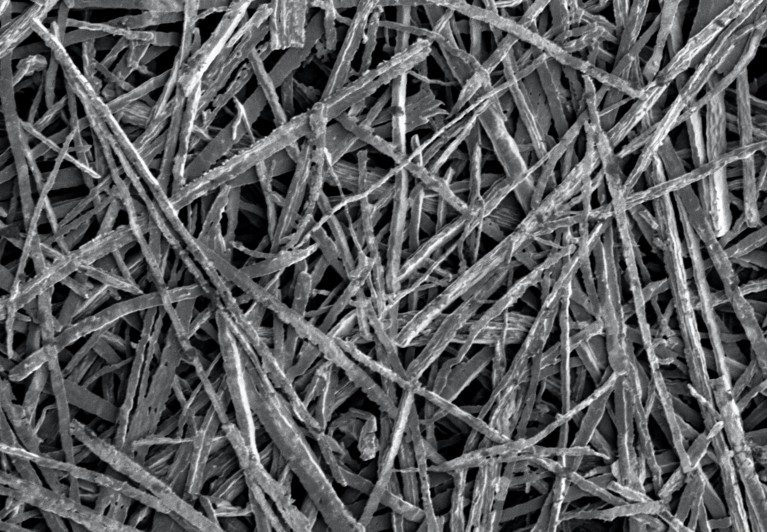
A scanning electron micrograph of a fibre sintered porous sheet (×25 magnification).© TOHO TITANIUM CO., LTD.
Moving downstream
Toho Titanium’s expertise in electrical-based deposition methods is paying off when it comes to innovative new products. The company has developed a technique for growing paper-sized thin titanium films directly onto cathodes without any rolling or annealing, and they can be separated by hand. The team can produce powder or fibre sintered porous sheets of about a metre long for use in parts of hydrogen-energy systems. The new smelting technology contributes to greener manufacturing of those high-functioned products.
“Our customers are thinking about ways to reduce their carbon footprints — not only from things like fuel, but also from the materials used to construct their products,” says Fujii. “Using our titanium smelting technology, Toho Titanium is aiming to reduce carbon dioxide emissions by 40% in 2030 from the 2018 level and to achieve carbon neutrality in 2050.”